The droplet size is strongly dependent on the continuous phase flow rate and the sizes of both the dispensing nozzle and the flow-focusing orifice. In this review, we will report the results of Rahimi’s publication on the effect of the nozzle size on the size of generated droplets. In this study, they evaluated the effects of multiple local geometries on droplet formation in a microfluidic co-axial flow-focusing device numerically with experimental validations. Then, we will present an ingenious work on exchangeable microfluidic nozzles to obtain various monodisperse droplets easily.
Influence of the nozzle geometry on the droplet size
Among the different geometries for droplet generation (flow focusing, T-junction, co-flow), the best monodispersity is obtained with flow focusing and co-flow. Generally, they are composed of a nozzle containing the fluid of the dispersed phase embedded in a rectangular or axisymmetric channel containing the shear fluid of the continuous phase. A contraction zone downstream of the nozzle is used in flow-focusing devices to change the hydrodynamic behavior of the flow field and thus the formation of droplets.
Numerically, Rahimi and his collaborators used the scheme presented in Figure 1 to distinguish 2 groups of geometric parameters considered to be effective in the droplet formation process. The first group includes the inner radius of the dimensionless nozzle (R1*=R1/R2) and its distance from the orifice inlet (L2*=L2/R2). The radius of the dimensionless orifice (Ro* = Ro/R2) and its length (Lo* = Lo/R2) have been classified in the second group to reflect the flow focusing specifications.
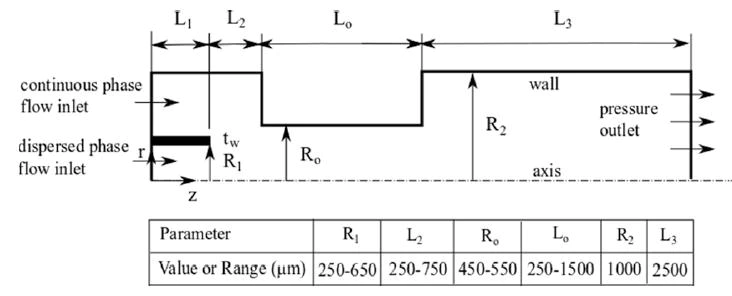
It was possible to measure the diameter of generated droplets according to the different nozzle sizes and for a fixed capillary number.
When the size of the jet is proportional to that of the nozzle, the size of the jet is then affected by the hydrodynamic forces of the flow. Thus, a narrow jet is established inside the focusing orifice, i.e. downstream of the nozzle. But the size of the water jet in the larger nozzle is comparatively larger in diameter and length due to the higher water flow rate in this condition (Figure 2A).
Consequently, a larger droplet forms at the end of the water jet when using a larger nozzle which is experimentally verified (Figure 2C).
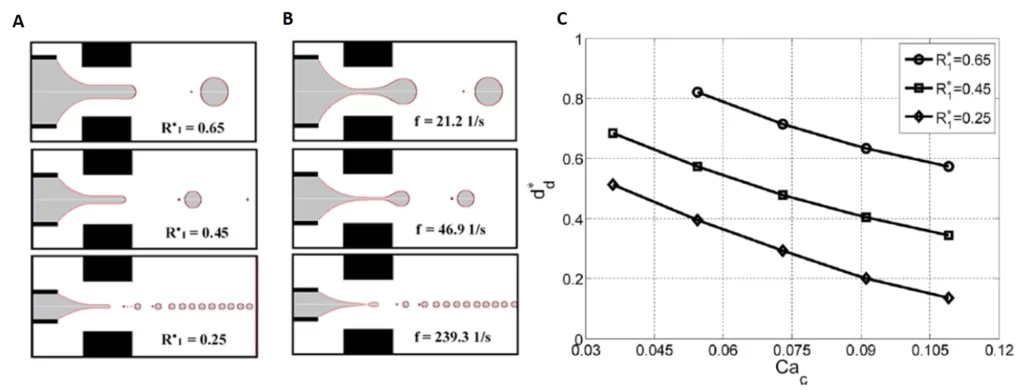
In addition, the droplet generation rate when using different nozzle sizes shown in Figure 2B shows that very monodisperse droplets can be generated with a high flow rate using the smallest nozzle.
How do exchange microfluidic nozzles to easily obtain various monodisperse droplets?
In this section, we will briefly present the work published by Kamperman and his collaborators in 2020. They have created a concept of interchangeable nozzles that operate in a transparent 3D microfluidic device that can be reused. The easy exchange and repositioning of the nozzles make it possible to produce monodisperse water-in-oil and oil-in-water emulsions, solid microspheres, and even micromaterials with controlled diameters ranging from 10 to 1000 µm using a single microfluidic device.
Rahimi’s work showed us that the size of the nozzle was an important element in determining the generated droplet. Kamperman’s work shows us how, among other things, to vary very easily the size but also the composition of the generated droplet.
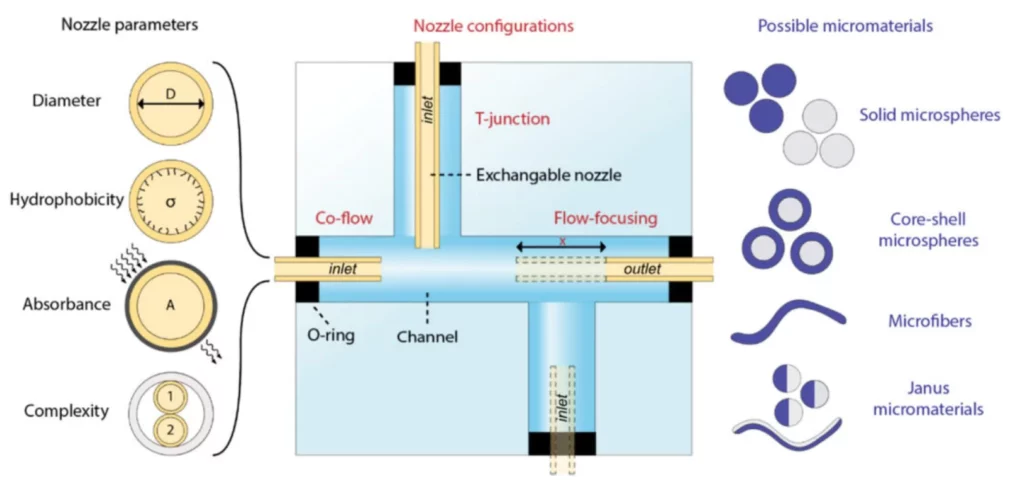
Leak-proof connections between the device, tubing, and nozzles allow the nozzles to be replaced on demand.
This makes it possible to change nozzles of different diameters, hydrophobicity, absorbency, and complexity in less than a minute. In addition, nozzle placement can be controlled over time to change from a T-junction configuration to a co-flow or even to a flow-focusing configuration. The multifunctional nature of this microfluidic device allows it to be easily adapted to the manufacture of various micro-materials, including emulsions, microspheres, and microfibers.
🧠What you have to remember
• Flow-focusing devices use a contraction zone downstream of the nozzle to change the hydrodynamic behavior of the flow field, resulting in monodispersed droplets.
• The best monodispersity is achieved with flow focusing and co-flow geometries, which typically consist of a nozzle containing the dispersed phase fluid embedded in a channel that holds the shear fluid of the continuous phase.
• The multifunctional nature of Kamperman microfluidic device makes it suitable for producing various micro-materials such as emulsions, microspheres, and microfibers with adjustable nozzle placement in configurations such as T-junction, co-flow, or flow-focusing.