In this review, we will discuss the different coating methods to generate droplets in a microfluidic device. There are mainly two types of coating: hydrophobic and hydrophilic. Regardless of the type of coating to be applied, two parameters must be taken into account: the physical and chemical properties of the material used to manufacture the microfluidic device, and whether you wish to make oil-in-water droplets or water-in-oil droplets.
Why the wettability of my chip matters?
To efficiently generate droplets, the continuous phase must effectively wet the walls of the microfluidic device. Let’s take the example of water-in-oil droplets (w/o): oil being the continuous phase, the channels should be hydrophilic so the oil will wet the walls.
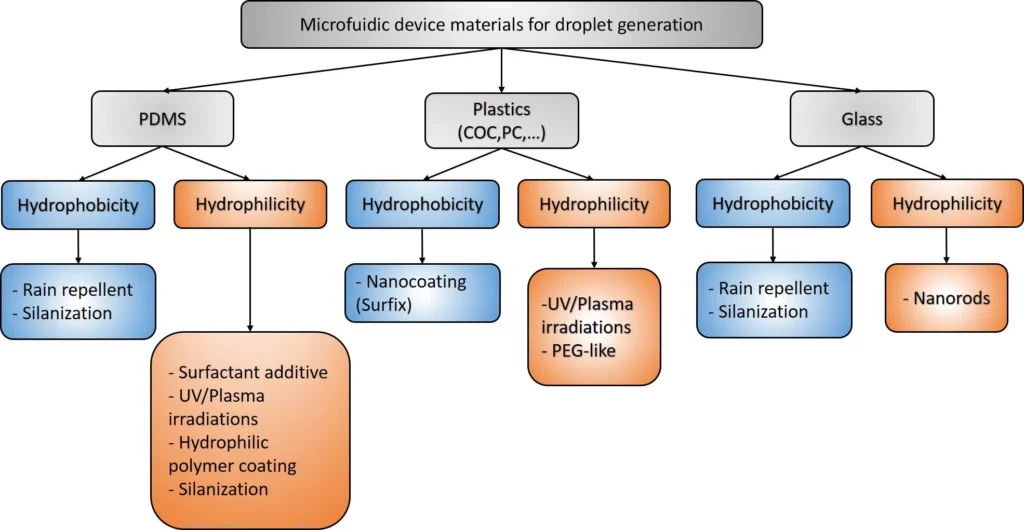
Materials in microfluidics and popular coatings
PDMS
The most popular biomaterial used in microfluidics is of course PDMS. Its numerous physicochemical properties, compatible with cell culture and microfabrication, have made it extremely popular. Among its many properties, we will focus on its highly hydrophobic nature which has consequences for droplet-based microfluidics and makes PDMS an ideal material for the generation of water-in-oil (w/o) droplets.
Hydrophobic coatings
To reinforce the hydrophobicity of PDMS, it is recommended to use a rain repellent such as Aquapel® or silanize the substrate.
The silanization consists of the reaction between silanol groups on SiO2 surfaces and alkoxysilanes forming a stable covalent bond. Silanes are employed for SiO2, and subsequent covalent reactions to binding other entities occur depending on the employed silane head group. The use of silanes (and more precisely, fluorosilanes) is commonly used in the generation of droplets when using PDMS or glass microfluidic devices.
Aquapel® is originally a rain repellent that makes materials such as glass completely hydrophobic. It is therefore particularly suitable for the generation of water in oil droplets with microfluidic glass devices or to make PDMS even more hydrophobic. Actually, any other rain repellent containing silicone and isopropanol can also be used such as TurtleWax® for example. In practice, the channels must be filled with the rain repellent first and left to rest for 1 minute. Afterward, it is recommended to rinse with air. The channels should be filled with the rain repellent a second time (1 min). Rinse again with air. The oil in which the droplets are generated can be used to properly rinse the channels to remove any Aquapel residue (an important step to minimize cytotoxicity when working with cells). Rinse again with air and then place the treated PDMS device in an 85°C oven for 10 minutes to dry completely.
Hydrophilic coatings
Due to its high hydrophobicity, PDMS completely prevents the formation of oil-in-water (o/w) droplets without prior surface treatment. However, the generation of oil-in-water droplets is necessary for a wide variety of applications such as the encapsulation of single cells in double emulsions, and the formation of vesicles or other model membranes to name a few. To meet this need to make PDMS hydrophilic, several techniques have been developed such as UV or plasma irradiations, a coating with a hydrophilic polymer, or the incorporation of an amphiphilic surfactant in the PDMS bulk.
To be more precise, the technique of UV or plasma irradiation consists of the oxidation of the polymer surface with plasma irradiation or ultraviolet (UV). The oxygen modification shows hydrophilic stability in the range of 2 days at the power of 150 W and exposure time of 15 min.
For the coating with a hydrophilic polymer, the method is based on coating channels with PVA immediately after plasma treatment. It is recommended to modify the surface by exposing the oxidized PDMS surfaces to 1% by weight PVA plasma in water for 10 minutes. O2 plasma creates alcoholic hydroxyls (C–OH), silanols (Si–OH), and carboxylic acids (COOH), which allow hydrogen bonding between the PVA molecules and the activated PDMS surfaces, which leads to permanently hydrophilized surfaces. In addition, a multilayer PVA assembly is facilitated through hydrophobic interactions between the main chain groups (–CH2–CH–) and the intermolecular hydrogen bonding of the γ–OH hydroxyl groups between the absorbed PVA after drying out the PDMS surface and the PVA chain in aqueous solution.
The incorporation of an amphiphilic surfactant in the PDMS bulk is considered as a surfactant added into the PDMS base and the curing agent mixture during polymerization to create hydrophilic poly(dimethylsiloxane-ethylene oxide polymeric (PEO-PDMS). The hydrophilicity will remain stable for two months and then slightly varied later. However, given the price of the surfactant, using this method for routine stuffing of microfluidic devices is unsustainable in the long term.
🧠What you have to remember:
• Aquapel® is a rain repellent that makes materials such as glass completely hydrophobic, making it suitable for the generation of water in oil droplets with microfluidic glass devices or to make PDMS even more hydrophobic. It is recommended to fill the channels with rain repellent; let it sit for 1 min, rinse with air and repeat the process. To dry the device, you can heat it in an oven at 85°C for 10 minutes to dry completely.
• UV or plasma irradiation is a technique used to make PDMS hydrophilic by oxidation of the polymer surface with plasma irradiation or ultraviolet (UV). It has been shown that this modification allows for stable hydrophilicity in the range of 2 days.
• PVA coating is another method for making PDMS surfaces hydrophilic. It involves coating channels with PVA immediately after plasma treatment and exposing the oxidized PDMS surfaces to 1% by weight PVA plasma in water for 10 minutes.
• Amphiphilic surfactants are also used to create hydrophilic PDMS by adding them to the PDMS base and curing agent mixture during polymerization. However, given the price of these surfactants, they may not be suitable for the routine coating of microfluidic devices.
COC, PC and PMMA
Plastics are also compatible with many of the same surface treatments than PDMS and glass, enhancing their versatility for applications requiring surface functionalization. Most commercially available plastics are hydrophobic in their native form, which can result in the adsorption of molecules and influence the accuracy of analytical measurements. Various methods have been reported to make plastic surfaces more hydrophilic [Lin et al. 2017, RSC Adv] or reinforce their hydrophobicity.
Hydrophilic coatings
Various methods have been reported to make plastic surfaces more hydrophilic, such as oxygen plasma etching and UV/ozone (UVO) exposure. In their work, Lin et al. showed in 2017 that UVO-treated PMMA, COC and PC experience hydrophobic recovery within 4 weeks and the rate at which it occurs is dependent on the UVO treatment duration. Furthermore, they have discovered that the hydrophobic recovery of UVO-treated COC and PC can be inhibited by storing them in dehumidified or vacuum conditions.
Recently, a new type of hydrophilic coating has been developed. In this process, the surface is modified using a PEG-like coating. Both exposed glass and polymer surfaces (COC, polycarbonate, PMMA) can be coated with this substance. The coating is applied using the plasma enhanced chemical vapor deposition (PECVD) technique. In this method, the surface is covered with a very thin film that transforms from a gas state (vapor) to a solid state [Micronit website].
Hydrophobic coatings
Concerning the reinforcement of the hydrophobicity of the COC, a hydrophobic 3D nanocoating was developed which leads to enhanced hydrophobicity of COC (contact angle 125°). Moreover, it was demonstrated that the nanocoatings are compatible with typical conditions for thermal compression bonding [Surfix website].
Glass
Unlike hydrophobic materials, it is easy to generate oil-in-water droplets in materials such as glass. It will therefore be necessary to carry out a surface treatment in order to generate water-in-oil droplets efficiently (Figure 1) or enhance the hydrophilicity to generate oil in oil in water droplets.
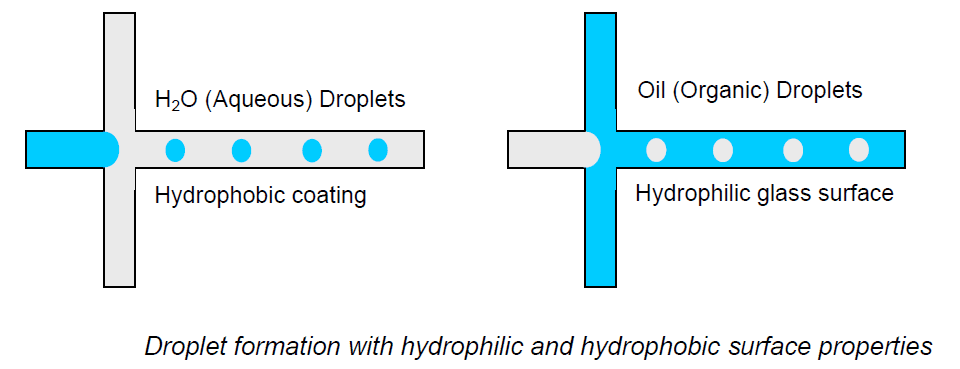
Figure 1 : Formation of water in oil droplet and oil in water droplet in microfluidic glass device. Extracted from the Droplet Chip User Guide of Dolomite-Microfluidics
Hydrophilic coatings
Khoshmardan et al. reported in 2019 a new technique to enhance hydrophilicity of glass microfluidic device. Nanorods are deposited on glass microchannel surface in order to enhance capillary force. The outer surfaces of these nanorods contribute to the capillary phenomenon and, on the other hand, they are hydrophilic due to being oxidized and attracting fluid molecules, thereby the fluid easily and rapidly moves between nanorods. The fluid molecules move from nanorod to nanorod, and thus the fluid inside the microchannel on the glass chip can easily flow by the capillary force.
Hydrophobic coatings
Finally, there are two main ways to make a glass microfluidic device hydrophobic: the use of a rain repellent or silanization, two methods described above.