Proper handling of the Bartels BP7 micropumps is essential to ensure their optimal performance and longevity. These piezoelectric micropumps, developed by Bartels Mikrotechnik, represent a breakthrough in microfluidic technology, providing a compact, efficient, and reliable solution for managing liquids and gases. However, to fully unlock their potential and prevent common operational issues, users must follow specific guidelines regarding installation, commissioning, operation, and maintenance.
While the BP7 manual provides valuable insights, some crucial tips and instructions (🚨) may be overlooked when skimmed. In this blog post, we will highlight these important aspects (mechanical, electrical, fluidic, and software-related tips), offering practical guidance to help you not only comply with general instructions but also troubleshoot some problems.
⚙️ Mechanical Instructions for the BP7 Micropump
Handling the Flex Cable
🚨 The BP7 micropump’s flex cable is delicate and should be handled with care. Avoid bending or twisting it, especially around sharp edges, to prevent damage. Secure the micropump and plug connection to reduce mechanical stress from vibrations.
🚨 The connector is rated for about 30 connection/disconnection cycles, so replace it regularly to ensure reliable performance.
🚨 Do not modify the flex cable, as doing so can compromise the functionality and void the warranty.
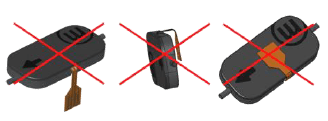
Pump Compatibility
🚨 The BP7 micropump’s performance may be affected by the absorption of liquid molecules, which can alter the mechanical properties of its internal components. While this change can impact the pumping process, it is important to note that the effect is reversible, and the pump is not permanently damaged.
The table below shows the compatibility of the pump with different liquids after long-term measurements for two weeks at 250Vpp/100Hz.
Chemical Substance | Concentration (%) | PPSU Chemical Compatibility |
---|---|---|
Acetic acid | 100 | F |
Acetone | 100 | X |
Cleaning gasoline | 100 | F |
Ethanol | 100 | X |
Ethyl acetate | 100 | X |
Glycerin | 60 | E |
Isopropanol | 100 | F |
Methanol | 100 | X |
Sodium hydroxide | 0.2 | E |
Vacuum pump oil | 100 | G |
E = Excellent; Little to no effect.
G = Good; No serious loss of properties.
F = Fair; Some negative effects, some useful properties retained.
X = Poor; Sever attack or rupture.
Chemical Compatibility of PPSU
The BP7 micropump body, made from PPSU (Polyphenylsulfone), offers excellent resistance to diluted acids, alkali solutions, and many organic solvents. However, it is less resistant to concentrated acids and ketones. For detailed chemical compatibility, refer to our comprehensive guide.
⚡ Electrical Instructions for the BP7 Micropump
Connection and Handling Precautions
Misconnection or improper handling can result in pump or electronics failure. Therefore, it is essential to maintain a secure connection between the micropump and the board connector.
🚨 When attaching the pump driver (mp-Lowdriver, mp-Highdriver, mp-Highdriver4, mp-Driver, mp-Valvedriver), align the white dot on the top left corner of the driver with the white marker on the mp-Multiboard2 to properly locate Pin 1.
🚨 Handle the pump driver carefully when removing it to avoid bending the pins and affecting functionality.
🚨 Limit the wire length between the controller and the pump to a maximum of 1 meter to ensure optimal performance.
🚨 Insert the pump cable with the contact surfaces facing down into the plug; incorrect orientation will prevent the pump from functioning. Secure the connection by closing the white plug. To disconnect, open the Molex connector first.
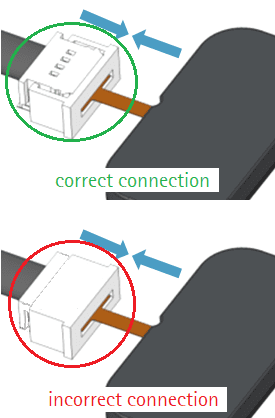
Protection from Environmental Factors
🚨 Ensure the ground is properly earthed before applying supply voltage to prevent damage, as driver chips are sensitive to electrostatic discharge.
🚨 Avoid touching the controls during operation, as they operate at high voltages, and contact may lead to injury or equipment damage.
🚨 Prevent any contact between the micropump’s flex cable, connectors, or electronics with liquids or moisture, as this may lead to short circuits and pump failure.
Power and Temperature Management
🚨 If more current is required, connect an external power supply through the USB-C connector.
🚨Ensure the Highdriver platform operates below 160°C to prevent it from entering non-operational mode.
🚨Use square-edged rectangular signals briefly to avoid excessive mechanical stress on the piezoactuators, which can lead to pump failure.
💻 Software-Related Instructions for the BP7 Micropump
Channel Detection and Activation
After successfully installing the USB driver, the Multiboard2 App will automatically detect the connected driver and enable the appropriate channels:
- Highdriver4: Enables channels CH1 through CH4.
- mp-Highdriver: Allows control of channel CH5 only.
- mp-Lowdriver: Allows control of channel CH5 only.
- mp-Driver: Enables channel CH6 only.
🚨 For instance, while using the Lowdriver to control one BP7 pump, this pump should be connected to CH5 on the Multiboard2.
USB Driver Installation (Windows)
🚨 If your PC does not automatically recognize the ESP32 microcontroller, you will need to install the USB driver manually. Follow these steps:
- Visit the Bartels website and go to the Download section.
- Download the mp-Multiboard2_USB_Driver.zip file.
- Unzip the file and right-click on the silabser.inf setup information file.
- Select Install from the context menu to install the drivers on your device.
💧 Fluidic Instructions for the BP7 Micropump
Tubing Connection
🚨 Connect suitable tubes to the inlet and outlet of the BP7 micropump. Bartels Mikrotechnik recommends using Tygon LMT-55 for water-based solutions or F4040 for solvents, both with an inner diameter (ID) of 1.3 mm and an outer diameter (OD) of 3 mm.
Parallel and Series Connections
🚨 Configure the BP7 micropumps in either parallel or series connections based on application requirements:
- For higher throughput, connect multiple pumps in parallel to increase the total flow rate.
- For applications that require elevated pressure, connect pumps in series to increase the system’s maximum pressure.
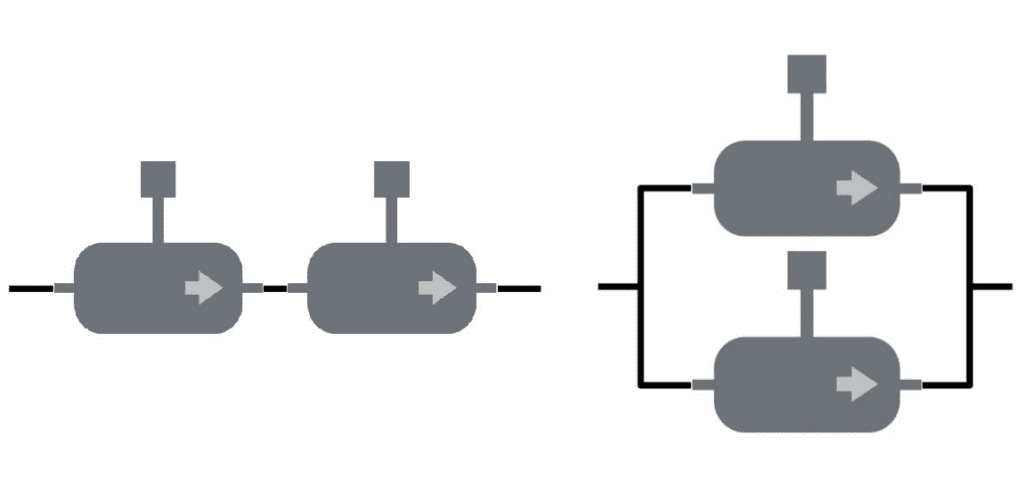
Cleaning the Micropump
🚨 To thoroughly clean the BP7 micropump, use Isopropyl alcohol (IPA). You can either draw IPA through the system using a syringe from the outlet or run the micropump with IPA or ethanol for several minutes. After cleaning, flush the micropump with distilled water to remove any residual alcohol from the pump channels and chambers.
🚨 Always flush in the pump’s operating direction, as negative pressure at the outlet is preferred over positive pressure at the inlet.
🚨 Always rinse or fill the BP7 micropump from the outlet (suctioning) to avoid exceeding the maximum pressure of 1 bar, which can cause pump malfunction.
🚨 Handle the micropump in a clean environment and use filters to prevent contamination. Ensure only liquids with particle sizes smaller than 50 μm are pumped, as larger particles can impair functionality.
Priming the Micropump
🚨 To prime the BP7 micropump for transporting liquids and gases:
- Start with the highest voltage and a frequency of at least 300 Hz to remove air from the system. Once the liquid reaches the micropump, reduce the frequency to 100 Hz for optimal performance.
- For manual priming, apply negative pressure at the outlet using a syringe or connect an external pump (e.g., a second BP7) to prime the first BP7.
Conclusion
Handling the BP7 micropump with care is key to getting the best out of it. By paying attention to the tips and instructions—whether it’s making secure connections, keeping the pump clean, or setting it up correctly—you’ll ensure smoother operation and a longer lifespan. Simple steps can make a big difference. With these practical tips, you can avoid common issues and get the most from your BP7 micropump in any application.
For a more detailed overview of the BP7 micropump, its full range of features, and system components, check out our Bartels BP7 overview blog. You’ll also find other helpful guides in this series, including detailed posts on topics like the mp-Multiboard2 and mp-Drivers, and more about controlling the BP7 with the Multiboard2 App.
📧 If you have any questions or feedback, please feel free to contact us at support@darwin-microfluidics.com.