The step emulsification is a variant of the droplet generation technique called co-flow. This new technique is based on the instability of a two-phase liquid wire triggered by an abrupt change in the flow confinement (Figure 1). It is more directly inspired by microchannel emulsification since it uses microfabricated channel networks that allow remarkably tight geometric control of the droplet size.
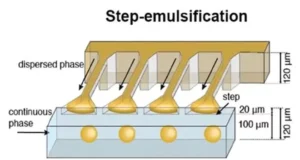
Mechanism of step emulsification
The step emulsification technique is used to generate droplets with diameters ranging from nanometers to hundreds of micrometers. To carry out this process, the necessary equipment consists of a dispersed phase channel, a reservoir of the continuous phase, and a nozzle, with a height that is significantly different from the reservoir.
To characterize this technique, several geometric models have been established. Among these models, it is the quasi-static mechanism that has been retained by most researchers to understand how the drops are generated. According to Dangla et al. 2013 J Phys D Appl Phys, this model is conditioned by three hypotheses:
- the dispersed phase is not able to wet the channel walls for droplet formation,
- gravitational effect is negligible,
- the system evolves in a quasi-static manner.
To successfully generate droplets by step emulsification, the continuous phase containing the surfactant must be injected first in order to fill the reservoir. The dispersed immiscible phase is then injected into the channel. Thus, as the thread of the dispersed phase passes through the step, a bulb emerges downstream of the step. As the dispersed phase is continuously injected, the average curvature of the blub decreases, while its size increases (Figure 2).
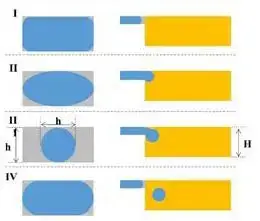
Types of step emulsification designs
The grooved-type microchannel emulsification step is governed by interfacial tension for droplet formation when using pressure or flow rate. Classically, the grooved microchannel includes a dispersed phase channel, a nozzle, a terrace and a continuous phase reservoir (Figure 3a). This kind of device can be manufactured on a silicon wafer by photolithography and orientation-dependent etching.
A second example is the use of a straight microchannel for stepwise emulsification, the structure of which includes elongated straight holes for the formation of droplets (Figure 3b). The droplet diameter is linearly related to the depth of the straight hole, which is roughly a multiple of 4. For the manufacture of this device, deep reactive ion etching (DRIE) on a silicon wafer can be used.
Another step emulsification structure allowing the generation of droplets at high flow rates is the Edge Droplet Generation Device (EDGE). This time it will no longer be a straight hole but a wide, shallow plateau as a nozzle, in which parallel droplets are generated simultaneously from a single nozzle (Figure 3c). To make this device, a silicon wafer is etched using the deep reactive ion etching (DRIE) technique and then bonded with a glass plate.
So far, only rectangular nozzles have been used in the above-mentioned devices. However, triangular nozzles have demonstrated much better performance. The triangular nozzle then acts as a terrace for the backflow of the continuous phase with the stretched cross-section (Figure 3d). In this way, the triangular nozzle provides an independent local area for the formation of droplets in order to avoid unwanted interference of the dispersed and continuous phases.

In step emulsification, it is important to note that the size of the monodisperse droplets is related to the geometrical characterizations of the microchannel, which means that the droplet diameter is difficult to adjust once the microchannel is designed.
Although limited in droplet size by geometry, step emulsification is a robust tool especially when combined with detection, identification and information technologies, which will improve the measurement of bioinformation.
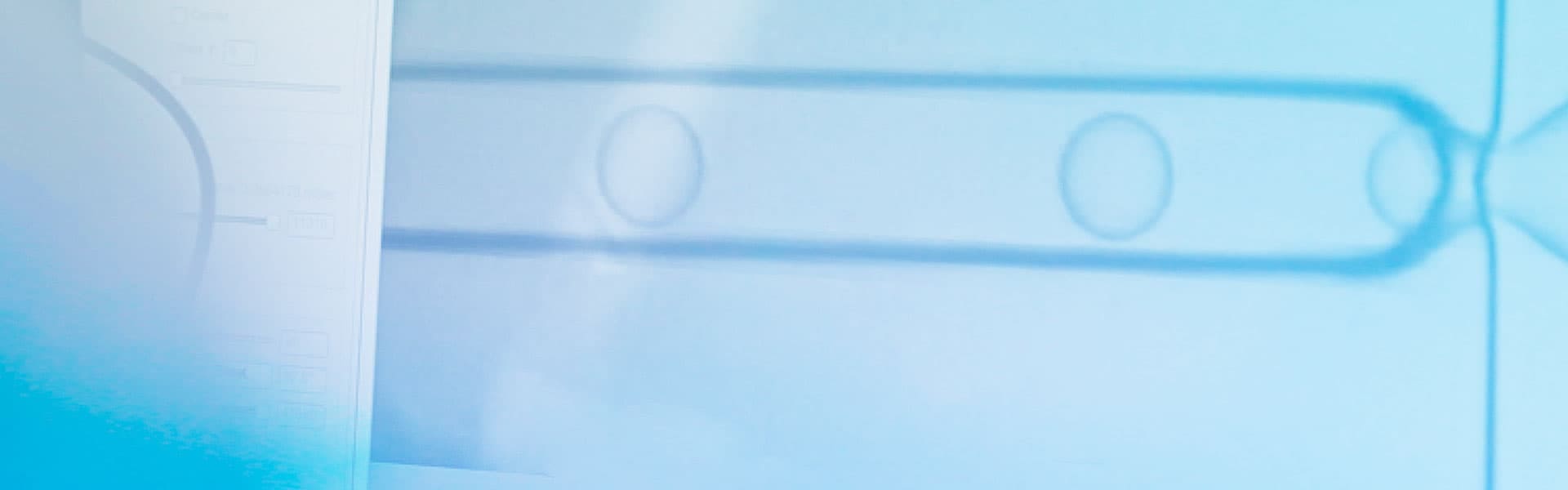