As the development of microfluidic devices, such as cell culture chips and organs-on-chips, continues to grow, sterilization becomes a critical step for maintaining the integrity of these systems. Any equipment coming into contact with sensitive biological fluids must be thoroughly sterilized to ensure the viability and reproducibility of experimental results. Although several sterilization methods exist, autoclaving (or steam sterilization) remains the most popular choice due to its effectiveness, simplicity, low cost, and environmentally friendly nature—producing no toxic residues.
This review introduces the various types of autoclaves, discusses their mechanisms, and identifies the materials most compatible with this sterilization method.
How Does Autoclave for Sterilization Work?
Autoclaving relies on heat sterilization, a straightforward process that involves exposing devices to saturated steam at 121°C for 20 minutes under a pressure of 115 kPa. The high heat causes protein denaturation, effectively disrupting microbial activities and ensuring sterilization. However, if conditions are not optimal, microbial activity might temporarily halt but resume once the temperature drops.
For successful germ destruction, the steam used must be homogeneous and saturated, with the high temperature generating a corresponding pressure, as dictated by Regnault’s law. It is essential to use demineralized water to produce steam, as this prevents any suspended substances from contaminating the system.
A typical autoclaving cycle (as the one represented in the figure below) includes:
- Pre-sterilization phase: Multiple steam injections alternate with vacuum injections to purge air from the sterilization chamber. The absence of air ensures better steam penetration.
- Sterilization phase: The chamber is maintained at a target temperature and pressure for a set duration (e.g., 121°C for 20 minutes).
- Cooling phase: After sterilization, the chamber cools down, and pressure decreases until it reaches atmospheric levels.
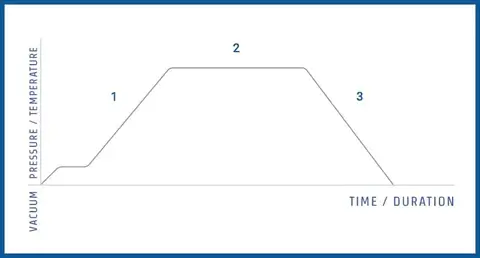
Different Types of Autoclaves
Autoclaves are categorized into three main types: Class N, Class B, and Class S. Understanding their differences is essential to selecting the best autoclave for specific applications, particularly in microfluidics.
Class N Autoclave
The Class N autoclave is designed for simple solid products (referred to as "naked solid products") and cannot effectively sterilize textiles, porous materials, hollow items, or products in sealed containers. A notable limitation is its inconsistent steam penetration, primarily because it does not require vacuum pre-conditioning. As a result, Class N autoclaves are best suited for straightforward, non-porous materials.
Class B Autoclave
Class B autoclaves, also known as "big small sterilizers," are compact yet highly efficient, capable of sterilizing a wide range of materials. This includes porous materials, textiles, hollow objects like glass syringes, and sealed products. The EN 13060 standard defines their performance and cycles, making them a reliable choice for medical and microfluidic applications. Their versatility and small size make them the preferred option for microfluidics.
Class S Autoclave
Class S autoclaves fall between Class N and Class B in terms of functionality. These machines vary significantly in performance since they are not bound by a specific standard, with their sterilization capabilities determined by the manufacturer. As such, they are less commonly used for precise applications like microfluidics.
Choosing the Right Autoclave for Microfluidics
Given the sensitive nature of materials and devices used in microfluidics, the Class B autoclave emerges as the most appropriate choice. Its versatility, capacity to handle a wide variety of materials (including porous and hollow items), and adherence to strict safety standards make it well-suited for microfluidic sterilization processes.
Autoclavable Materials in Microfluidics
Determining which materials can withstand the high temperatures (121°C) and pressures used in autoclaving without suffering damage is a significant challenge in microfluidics. While many common microfluidic materials are autoclavable, several others, such as PMMA, PVC, and PC, are often mistakenly assumed to be suitable for autoclaving when they are not. This is due to their glass transition temperatures (Tg) being below 121°C, which means these materials could potentially melt or deform during the process. Therefore, it is essential to verify the thermal properties of each material before sterilization to avoid damage.
To ensure the efficiency and safety of your microfluidic system, refer to the table below for informed decisions about which materials are truly autoclavable.
Additionally, always consult the manufacturer’s instructions for specific guidance on the compatibility of individual components—whether you are working with tubing, chips, or connectors—before proceeding with any sterilization procedure.
Material | Autoclavable ? |
---|---|
316 Stainless Steel | Yes |
Acrylic | Yes |
Borosilicate glass | Yes |
Delrin (Polyoxymethylene) | Yes |
ETFE (Ethylene Tetrafluoroethylene) | Yes |
FEP (Fluorinated Ethylene-Propylene) | Yes |
Halar | Yes |
High Purity PFA | Yes |
Nylon | No |
PC (Polycarbonate) | No |
PCTFE (PolyChloroTriFluoroEthylene) | Yes |
PDMS (Polydimethylsiloxane) | Yes |
PEEK (Polyetheretherketone) | Yes |
Perlast | Yes |
PFA (Perfluoroalkoxy) | Yes |
PK (Polyketone) | Yes |
PMMA (Polymethyl Methacrylate) | No |
PE (Polyethylene) | No |
Polysulfone | Yes |
PP (Polypropylene) | Yes |
PPS (Polyphenylene Sulfide) | Yes |
PS (Polystyrene) | No |
PTFE (Polytetrafluoroethylene) | Yes |
PVC (Polyvinyl Chloride) | No |
Radel® | Yes |
Silicone | Yes |
Soda–lime glass | No |
Titanium | Yes |
Topas - COC (Cyclic Olefin Copolymer) | No |
TPX® (Polymethylpentene) | Yes |
UHMWPE (Ultra High Molecular Weight Polyethylene) | No |
Ultem | Yes |
Vespel | Yes |
Zeonex - COP (Cyclic Olefin Polymer) | No |
Zeonor - COP (Cyclic Olefin Polymer) | No |
Conclusion
Sterilization is a vital step in microfluidics, particularly for biomedical and biological applications. Steam sterilization by autoclaving is a reliable and widely used method, provided the correct protocols are followed. By selecting appropriate autoclaves—such as Class B autoclaves—and ensuring the compatibility of materials, you can guarantee the safety and performance of your microfluidic devices.
Stay tuned for more insights, tutorials, and practical applications in our future posts. Until then, stay brave, autoclave, don’t let microbes misbehave 🧪🔬!
📧 If you have any questions or feedback, please feel free to contact us at support@darwin-microfluidics.com.